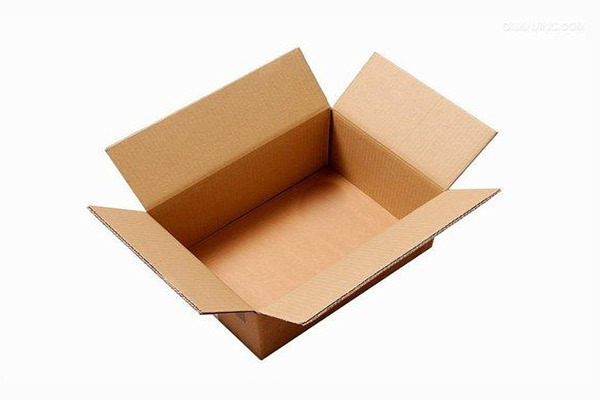
纸箱印刷过程中常出现色彩、套印、糊版、墨色等方面的问题,以下是对这些常见问题的分析:
色彩偏差
原因:印刷油墨的颜色调配不准确,未按照标准色卡或客户要求进行调配;不同批次的油墨存在色差;印刷设备的颜色管理系统设置不当,导致颜色输出不一致;承印材料的表面特性不同,对油墨的吸收和反射情况有差异,影响色彩呈现。
解决方法:严格按照标准色卡进行油墨调配,采用高精度的调色设备和技术;对不同批次的油墨进行颜色检测和校准,确保一致性;校准印刷设备的颜色管理系统,定期进行色彩检测和调整;根据承印材料的特性,选择合适的油墨和印刷工艺,必要时对材料进行预处理。
色彩饱和度不足
套印不准
原因:印刷设备的套准系统出现故障或未调整好,如齿轮磨损、皮带松弛等;纸张在印刷过程中发生变形或位移,可能是由于纸张的含水量不均匀、印刷环境温湿度变化较大等原因;印版安装不准确或在印刷过程中发生移位;操作人员在装版、调机时操作不规范,没有准确校准套印位置。
解决方法:定期检查和维护印刷设备的套准系统,及时更换磨损的部件;控制印刷环境的温湿度,确保纸张含水量稳定,对纸张进行预调湿处理;正确安装印版,并使用定位装置固定好,在印刷过程中加强对印版的检查;操作人员严格按照操作规程进行装版和调机,提高操作技能和责任心。
糊版
原因:油墨的粘度太高,流动性差,导致在印刷过程中不易转移,堆积在印版上形成糊版;印刷压力过大,使印版与承印材料之间的接触面积过大,油墨被过度挤压,造成糊版;印版表面的网点磨损或堵塞,使油墨无法正常转移,形成糊版;油墨中混入了杂质或干燥过快,也会导致糊版现象的发生。
解决方法:调整油墨的粘度,加入适量的稀释剂或增塑剂,提高油墨的流动性;适当降低印刷压力,根据印版和承印材料的特性,选择合适的压力值;定期检查和更换印版,对磨损或堵塞的网点进行修复或更换;过滤油墨,去除其中的杂质,同时控制油墨的干燥速度,可添加适量的干燥剂或抑制剂。
墨色不均匀
原因:油墨在墨槽中的分布不均匀,可能是由于墨泵故障、墨槽设计不合理等原因;印刷辊的表面不平整或磨损,导致油墨转移不均匀;印刷速度不稳定,时快时慢,影响油墨的转移量;承印材料的表面平整度不一致,对油墨的吸收量不同。
解决方法:检查和维护墨泵,确保油墨在墨槽中均匀分布,必要时改进墨槽的设计;定期检查和更换印刷辊,保证其表面平整光滑;稳定印刷速度,避免速度波动;对承印材料进行筛选和预处理,提高其表面平整度。